En omfattande guide om hur man ställer in ett svarvskärverktyg
Att ställa in ett svarvskärverktyg är en grundläggande färdighet för alla maskinister, speciellt när de har att göra med CNC-svarvar (Computer Numerical Control). Korrekt verktygsinställning är avgörande för att uppnå exakta och exakta bearbetningsresultat. I den här omfattande guiden kommer vi att fördjupa oss i de intrikata detaljerna om hur man ställer in ett svarvskärverktyg för CNC-svarvning. Från grunderna för svarvverktygskomponenter till avancerade tekniker för att optimera skärprestanda, den här artikeln syftar till att ge en omfattande förståelse av processen. I slutet av denna guide kommer du att ha de kunskaper och färdigheter som krävs för att ställa in ett svarvskärverktyg med självförtroende och precision, vilket säkerställer optimala resultat i dina CNC-svarvningsoperationer.
Förstå svarvskärverktyg
I bearbetningsvärlden är svarvskärverktyg oumbärliga komponenter för att forma och omvandla råmaterial till precisionskonstruerade delar. Oavsett om du arbetar med traditionella manuella svarvar eller avancerade CNC-svarvar, är det viktigt att ha en grundlig förståelse för svarvskärverktyg. I det här avsnittet kommer vi att fördjupa oss i egenskaperna, funktionerna och typerna av svarvskärverktyg.
Egenskaper för svarvskärverktyg
Svarvskärverktyg är designade för att utföra en mängd olika bearbetningsoperationer, såsom svarvning, ytbearbetning, spårning, gängning och mer. Dessa verktyg delar flera gemensamma egenskaper:
- Hårdhet: Svarvskärverktyg är vanligtvis gjorda av höghastighetsstål (HSS), hårdmetall eller andra specialiserade verktygsmaterial. Dessa material är valda för sin hårdhet, vilket gör att verktyget tål de höga temperaturer och tryck som genereras under skärning.
- Allra senaste: Skäreggen på ett svarvverktyg är den del som faktiskt tar bort material från arbetsstycket. Den är utformad för att vara skarp och exakt, och skäreggens geometri kan variera beroende på den specifika uppgift verktyget är avsett för.
- Skaft: Svarvverktygets skaft är den del som kläms fast i verktygshållaren. Det ger stabilitet och styvhet till verktyget under tiden bearbetningsprocess. Skaftdesign kan skilja sig beroende på typ av verktyg och tillverkarens specifikationer.
- Verktygshållare: Verktygshållaren är en avgörande komponent, speciellt vid CNC-svarvning, eftersom den säkert håller svarven på plats. Den måste ge stabilitet, precision och enkel justering för att säkerställa optimal verktygsprestanda.
- geometri: Skärverktygets geometri, inklusive spånvinkeln, frigångsvinkeln och spånbrytaren, spelar en viktig roll för att bestämma verktygets prestanda. Korrekt geometri är avgörande för att uppnå effektiv materialborttagning och spånavskiljning.
- Beläggning: Många svarvskärverktyg kommer med specialiserade beläggningar, såsom TiN (Titanium Nitride) eller TiAlN (Titanium Aluminium Nitride), för att förbättra verktygets livslängd, minska friktionen och förbättra prestandan.
Funktioner för svarvskärverktyg
Svarvskärverktyg utför flera grundläggande funktioner i bearbetningsprocessen:
- Materialborttagning: Den primära funktionen hos svarvskärverktyg är att ta bort material från ett arbetsstycke. Detta avlägsnande kan ske genom svarvning (roterande av arbetsstycket under skärning), vändning (skapa en plan yta) eller andra operationer.
- Dimensionell kontroll: Skärverktyg ansvarar för att den bearbetade delens dimensioner överensstämmer med önskade specifikationer. Exakt kontroll är avgörande för att uppnå exakta och konsekventa resultat.
- Ytfinish: Kvaliteten på ytfinishen bestäms av skärverktygets skärpa, geometri och de skärparametrar som används. Ett välskött och korrekt uppsatt skärverktyg bidrar till en jämn och fin ytfinish.
- Chipkontroll: Effektiv spånkontroll är avgörande för att förhindra spånansamling och upprätthålla en ren och säker arbetsmiljö. Spånbrytaren på vissa verktyg hjälper till att underlätta spånavlägsnandet.
- Effektivitet: Svarvskärverktyg är utformade för att göra bearbetningsprocesser effektiva och kostnadseffektiva. De hjälper till att minimera materialspill och optimera verktygets livslängd, vilket minskar produktionskostnaderna.
Typer av svarvskärverktyg
Svarvskärverktyg finns i en mängd olika typer, var och en skräddarsydd för specifika bearbetningsuppgifter. Här är några vanliga typer:
- Svarvverktyg: Dessa verktyg är mångsidiga och används för cylindriska svarvningsoperationer. De kan forma de yttre och inre ytorna på ett arbetsstycke.
- Tråkiga verktyg: Borrverktyg används för att förstora eller avsluta befintliga hål. De är designade för precision och noggrannhet vid hålbearbetning.
- Skiljeverktyg: Skiljeverktyg används för att separera ett arbetsstycke från ett större lager. De skapar definierade skiljelinjer med minimalt avfall.
- Trådverktyg: Gängverktyg används för att skära gängor på ett arbetsstycke. De finns i olika former och storlekar för olika gängningskrav.
- Spårverktyg: Spårverktyg skapar spår eller urtag på ett arbetsstycke, vanligtvis för att ta emot O-ringar, hållarringar eller andra funktioner.
- Framstående verktyg: Beläggningsverktyg är utformade för att skapa plana ytor på änden av ett arbetsstycke. De används ofta för att uppnå vinkelräta ytor eller ta bort material från en arbetsstyckesände.
Att förstå egenskaperna och funktionerna hos svarvskärverktyg är avgörande för att välja rätt verktyg för en specifik bearbetningsuppgift. Valet av skärverktyg kan avsevärt påverka kvaliteten och effektiviteten i bearbetningsprocessen, vilket gör det till ett avgörande beslut i alla svarvoperationer. Dessutom är korrekt underhåll och verktygsinställning avgörande för att säkerställa konsekventa och exakta resultat, vilket kommer att diskuteras mer i detalj senare i den här guiden.
Typer av svarvskärverktyg
Svarvskärverktyg finns i olika typer, var och en speciellt utformad för en viss bearbetningsuppgift. Att förstå dessa olika typer av skärverktyg och deras tillämpningar är avgörande för att välja rätt verktyg för ett visst jobb. Här är några vanliga typer av svarvskärverktyg:
Svarvverktyg:
- Verktyg med rund näsa: Används för generella svarvningsoperationer. Den har en rundad egg och är lämplig för både grovbearbetning och finbearbetning.
- Diamantverktyg: Uppkallad efter sin diamantformade skäregg är den idealisk för exakt bearbetning av olika material, inklusive metaller och plaster.
- Square-Nose Tool: Har en fyrkantig skäregg och används vanligtvis för vändning och axelsvarvning.
Tråkiga verktyg:Intern Boring Bar: Används för att förstora och avsluta befintliga hål i ett arbetsstycke. Den är designad för precision och kan skapa exakta inre mått.
Skiljeverktyg:Avskiljningsblad: Dessa verktyg används för att skära av ett arbetsstycke från ett större lager. De skapar en definierad avskiljningslinje med minimalt avfall.
Trådverktyg:
- Trådskärningsverktyg: Designad för att skapa yttre gängor på ett arbetsstycke. De finns i olika former och storlekar för olika gängningskrav.
- Trådjagarverktyg: Används för att jaga eller återställa befintliga trådar. Dessa verktyg används ofta för trådreparation.
Spårverktyg:Spårverktyg: Dessa verktyg skapar spår eller urtag på ett arbetsstycke, ofta för att rymma O-ringar, låsringar eller andra funktioner.
Framstående verktyg:Facing Tool: Används för att skapa plana ytor på änden av ett arbetsstycke. Det används ofta för att uppnå vinkelräta ytor eller ta bort material från en arbetsstyckesände.
Avsticknings- och spårverktyg:Kombinationsverktyg: Dessa mångsidiga verktyg är designade för både avstickning och spårskärning, vilket sparar tid och verktygsbyten.
Gängnings- och spårverktyg:Kombinationsverktyg för gängning och räffling: Idealisk för jobb som kräver både gängning och spårning på samma arbetsstycke.
Fasningsverktyg:Fasningsverktyg: Används för att skapa avfasningar eller fasade kanter på arbetsstycket. Fasningar används ofta för att förbättra utseendet och enklare montering av bearbetade delar.
Räfflade verktyg:Räfflade verktyg: Knurling är en process för att skapa ett strukturmönster på ett arbetsstycke, vanligtvis för förbättrat grepp eller estetik. Räfflade verktyg finns i olika mönster och utföranden.
Formverktyg:Formulärverktyg: Dessa verktyg är specialdesignade för specifika detaljgeometrier, som ofta används för att producera komplexa och icke-standardiserade former.
Specialverktyg:Profilverktyg: Används för att skapa komplexa profiler på ett arbetsstycke.
Vändnings- och svarvverktyg: Dessa är designade för både vändning och svarvning.
Avskärningsverktyg: Designad för att skära igenom arbetsstycket för att skapa separata delar eller ta bort överflödigt material.
Valet av rätt skärverktyg beror på faktorer som materialet som bearbetas, den önskade finishen, de erforderliga dimensionerna och den specifika operation som utförs. Det är viktigt att välja rätt verktyg och underhålla det korrekt för att säkerställa effektiv och exakt bearbetning. Korrekt val av verktyg, tillsammans med korrekt inställning och justering, är avgörande för att uppnå högkvalitativa resultat vid svarvoperationer.
Komponenter i ett svarvskärverktyg
Ett svarvskärverktyg är ett precisionsinstrument utformat för att forma, skära och ta bort material från ett arbetsstycke. För att förstå hur det fungerar och hur man ställer in det på rätt sätt är det viktigt att vara bekant med dess olika komponenter. Här är nyckelkomponenterna i ett svarvskärverktyg:
- Verktygshållare:Verktygshållaren är den del som håller skärverktyget på plats. Den fäster på svarvens verktygsstolpe och ger den nödvändiga styvheten och stabiliteten för bearbetningsoperationer. Verktygshållare finns i olika utföranden för att rymma olika typer av skärverktyg.
- Skaft:Skaftet är den del av skärverktyget som passar in i verktygshållaren. Den är vanligtvis cylindrisk och kläms fast i hållaren. Skaftets dimensioner och form kan variera beroende på verktygstyp och design.
- Allra senaste:Skäreggen är den vassa delen av verktyget som kommer i kontakt med och tar bort material från arbetsstycket. Kvaliteten på skäreggen och dess geometri påverkar avsevärt skärprestanda och ytfinish. Det är viktigt att behålla skärpans skärpa och precision.
- Föra in:Många moderna skärverktyg använder utbytbara skär, som vanligtvis är gjorda av hårda material som hårdmetall eller keramik. Dessa skär har skärgeometrin och är fästa i en ficka på skärverktyget. De kan roteras eller bytas ut när de blir slitna eller skadade, vilket förlänger verktygets livslängd.
- Verktygsnäsa:Verktygets nos är själva spetsen på skärverktyget där skäreggen och skäret (om sådant används) möts. Verktygets nos måste vara exakt positionerad och inriktad för exakt bearbetning. Vissa svarvskärverktyg har en justerbar verktygsnosradie för bättre kontroll över verktygets prestanda.
- Verktygsflank:Verktygsflanken är den sidoyta på skärverktyget som inte är en del av skäreggen. Rätt släppningsvinklar på verktygsflanken säkerställer evakuering av spån och minskar friktionen mellan verktyget och arbetsstycket.
- Verktyg Rake Face:Spånytan är den yta på skärverktyget som är vänd mot arbetsstycket. Spånytans vinkel och tillstånd påverkar spånbildningen och skärprocessens effektivitet. Spånvinkeln är en kritisk aspekt av verktygets geometri.
- Verktygsavlastningsvinkel:Reliefvinkeln är vinkeln mellan verktygsflanken och verktygets axel. Det säkerställer att skäreggen inte skaver mot arbetsstycket, vilket minskar friktion och värmeutveckling.
- Verktygets frigångsvinkel:Frigångsvinkeln är vinkeln mellan spånytan och arbetsstyckets yta. Det tillåter spån att flyta jämnt och förhindrar interferens mellan verktyget och arbetsstycket.
- Spånbrytare (om tillämpligt):Vissa skärverktyg, särskilt de som används för grovbearbetning, har en spånbrytare, ett spår eller skåra på spånytan. Spånbrytaren hjälper till att kontrollera spånbildningen och förbättra evakueringen av spån.
Korrekt montering, uppriktning och underhåll av dessa komponenter är avgörande för att uppnå exakt och effektiv bearbetning. Valet av skärverktyg och dess inställning måste skräddarsys för den specifika bearbetningsoperationen och det material som bearbetas. Regelbunden inspektion och underhåll av skärverktygets komponenter är också nödvändigt för att säkerställa konsekventa och högkvalitativa resultat.
Att välja rätt skärverktyg för jobbet
Att välja rätt skärverktyg är ett avgörande beslut i alla bearbetningsoperationer, eftersom det i hög grad påverkar kvaliteten, effektiviteten och precisionen i arbetet. Flera faktorer bör beaktas när man väljer lämpligt skärverktyg för ett specifikt jobb. Här är en guide för hur du väljer rätt skärverktyg för ditt bearbetningsprojekt:
1. Material för arbetsstycket:
Materialet du bearbetar är en av de mest kritiska faktorerna vid val av verktyg. Olika material har olika hårdhet, värmeledningsförmåga och nötningsförmåga. Tänk på följande:
- Hårdhet: Hårda material som härdat stål eller keramik kräver skärverktyg med hårda skäreggar, såsom hårdmetallskär, för att klara de höga skärkrafterna.
- Mjuka material: För mjukare material som aluminium eller plast kan höghastighetstål (HSS) eller andra verktygsmaterial vara tillräckligt.
2. Bearbetningsoperation:
Den specifika operationen du utför, såsom svarvning, fräsning, borrning, gängning eller spårning, kommer att diktera vilken typ av skärverktyg du behöver. Olika verktyg är designade för olika uppgifter, och att välja rätt säkerställer optimal prestanda.
3. Skärhastighet och matningshastighet:
Bestäm önskad skärhastighet och matningshastighet baserat på materialet och bearbetningsoperationen. Tillverkare av skärverktyg ger rekommendationer för dessa parametrar baserat på verktygets design och det material som bearbetas. Att följa dessa rekommendationer är avgörande för att uppnå önskat resultat.
4. Verktygsgeometri:
Tänk på skärverktygets geometri, inklusive spånvinkeln, släppningsvinkeln och verktygets nosradie. Verktygsgeometrin ska matcha materialet och typen av skärning. Till exempel är en positiv spånvinkel lämplig för mjukare material, medan en negativ spånvinkel är bättre för hårdare material.
5. Arbetsstyckets mått:
Arbetsstyckets storlek och dimensioner påverkar också valet av verktyg. Vissa skärverktyg är bättre lämpade för grovbearbetning för att snabbt ta bort bulkmaterial, medan andra är utformade för efterbehandling för att uppnå exakta dimensioner och ytfinish.
6. Ytfinishkrav:
Om du behöver en specifik ytfinish, välj ett skärverktyg med lämplig geometri och skärpa. Finbearbetningsverktyg är utformade för att ge en jämnare ytfinish, medan grovbearbetningsverktyg är mer effektiva för materialborttagning.
7. Verktygsmaterial:
Valet av verktygsmaterial är avgörande. Hårdmetall, snabbstål (HSS), keramiska och belagda verktyg har alla sina fördelar och begränsningar. Tänk på faktorer som verktygets livslängd, slitstyrka och kostnaden för verktygsmaterialet i ditt beslut.
8. Kylvätska och smörjning:
Fundera på om skäroperationen kräver kylvätska eller smörjning. Vissa material genererar överdriven värme under bearbetning och att använda rätt kyl- eller smörjmedel kan förlänga verktygets livslängd och förbättra skärprestandan.
9. Verktygsbeläggningar:
Många moderna skärverktyg kommer med specialiserade beläggningar som TiN (Titanium Nitride) eller TiAlN (Titanium Aluminium Nitride) för att förbättra slitstyrkan och minska friktionen. Välj ett verktyg med lämplig beläggning för din specifika applikation.
10. Kostnadsöverväganden:
Att balansera kostnaden för skärverktyget med dess prestanda och livslängd är avgörande. Även om premiumverktyg kan erbjuda längre verktygslivslängd och bättre prestanda, är det viktigt att hitta en balans som ligger i linje med ditt projekts budget.
11. Verktygshållare och maskinkompatibilitet:
Se till att det valda skärverktyget är kompatibelt med din svarv eller bearbetningscenters verktygshållarsystem. Verktygshållaren ska ge stabilitet och styvhet till skärverktyget under bearbetningsprocessen.
I slutändan kommer det rätta skärverktyget för jobbet att bero på en kombination av dessa faktorer. Rådgör alltid med verktygstillverkarens rekommendationer och överväg att söka råd från erfarna maskinister eller verktygsexperter om du är osäker. Korrekt val av verktyg och inställningar är grundläggande för att uppnå effektiva och exakta bearbetningsresultat.
Installation av svarvskärverktyget
Att sätta upp ett svarvskärverktyg för CNC-svarvning är en systematisk process som innefattar flera avgörande steg. Varje steg är avgörande för att säkerställa att skärverktyget är korrekt positionerat och inriktat, vilket i slutändan leder till exakt och effektiv bearbetning. Låt oss gå igenom processen steg för steg:
Steg 1: Förberedelse av svarven och arbetsstycket
Innan du kan ställa in skärverktyget är det viktigt att förbereda både svarven och arbetsstycket:
- Säkra arbetsstycket: Se till att arbetsstycket är ordentligt fastklämt i svarvchucken eller hylsan. Se till att den roterar mjukt utan att vibrera eller vibrationer.
- Säkerhet: Se till att alla säkerhetsåtgärder är på plats, inklusive användning av lämplig personlig skyddsutrustning (PPE) och rätt svarvinställningar.
Steg 2: Välj rätt verktygshållare
Verktygshållaren är en kritisk komponent i installationsprocessen. Välj lämplig verktygshållare baserat på faktorer som typen av skärverktyg, operationen som utförs och svarvens verktygsstolpsystem.
- Matcha verktygshållaren med skärverktyget: Se till att verktygshållaren är kompatibel med typen och storleken på det skärverktyg du tänker använda.
- Verktygshållarens styvhet: Välj en verktygshållare som ger stabilitet och styvhet. Detta är särskilt viktigt i applikationer med hög precision.
Steg 3: Montering av skärverktyget
Att montera skärverktyget innebär att det säkras i verktygshållaren och att det är stadigt och korrekt placerat:
- Säkra skärverktyget: Sätt in skärverktyget i verktygshållaren och dra åt eventuella klämmekanismer, såsom ställskruvar eller spännhylsor. Se till att verktyget hålls säkert.
- Orientering: Kontrollera att skärverktyget är rätt orienterat i förhållande till arbetsstycket. Verktyget ska placeras så att det går i ingrepp med arbetsstycket i önskad vinkel och djup.
Steg 4: Justera verktygshöjd och mittlinjeinriktning
Korrekt verktygshöjd och mittlinjeinriktning är avgörande för att uppnå exakta bearbetningsmått:
- Verktygshöjdjustering: Justera verktygets höjd för att passa in i svarvens spindelcentrumlinje. Använd en verktygshöjdmätare eller en teststång för att ställa in verktyget på rätt höjd.
- Mittlinjejustering: Se till att verktyget är i linje med svarvens spindelcentrumlinje. Felinriktning kan resultera i bearbetning utanför centrum, vilket påverkar detaljnoggrannheten.
Steg 5: Ställ in verktygets nosradiekompensation
För CNC-svarvning svarar verktygets nosradiekompensation för skärverktygets geometri. Detta är särskilt viktigt när du använder skärverktyg:
- Bestäm verktygets nosradie: Mät eller slå upp den exakta nosradien för skärverktyget du använder.
- Mata in radievärdet: I CNC-styrprogramvaran, mata in det uppmätta verktygsnosradievärdet för att säkerställa att maskinen kompenserar för verktygets geometri vid bearbetning.
Steg 6: Ställa in verktygsoffset
Verktygsoffset tar hänsyn till variationer i verktygsdimensioner och arbetsstyckesgeometri. De säkerställer att verktygets position är exakt justerad för bearbetning:
- Välj rätt verktygsoffset: Bestäm lämpligt verktygsoffsetvärde baserat på verktygets geometri och bearbetningsoperationen. Detta offsetvärde kompenserar för eventuella avvikelser.
- Ange offsetvärden: Mata in de valda offsetvärdena i CNC-styrprogramvaran. Dessa värden kommer att instruera maskinen om hur man justerar verktygets position exakt.
Under hela verktygsinstallationsprocessen, använd precisionsmätinstrument som mikrometrar, höjdmätare och mätklockor för att verifiera och finjustera verktygsinriktningen. Inspektera och underhåll skärverktyget regelbundet för att säkerställa att det förblir skarpt och i gott skick, eftersom ett väl underhållet verktyg bidrar till konsekventa och exakta bearbetningsresultat.
Att korrekt ställa in svarvskärverktyget i dessa steg är avgörande för att uppnå optimala resultat i CNC-svarvningsoperationer. Precision och uppmärksamhet på detaljer under verktygsinstallationen är nyckelfaktorer för att producera bearbetade delar av hög kvalitet.
Optimering av skärparametrar för CNC-svarvning
Att optimera skärparametrar är avgörande för att uppnå effektiva och högkvalitativa CNC-svarvningsoperationer. De fyra nyckelaspekterna att tänka på vid optimering av skärparametrar är hastigheter och matningar, skärdjup, skärvätskor och smörjmedel samt hantering av verktygets livslängd.
1. Hastigheter och flöden:
- a. Skärhastighet (ythastighet):Skärhastighet, ofta kallad ythastighet, är den hastighet med vilken arbetsstycket och skärverktyget samverkar. Den mäts i ytfot per minut (SFM) eller meter per minut (m/min). För att optimera skärhastigheten, beakta materialet som bearbetas och verktygets material. Höghastighetstål (HSS) verktyg har lägre rekommenderade skärhastigheter än hårdmetallverktyg, till exempel. Se verktygstillverkarens data eller bearbetningshandböcker för att fastställa rekommenderade skärhastigheter för specifika material och verktyg.
- b. Inmatningshastighet:Matningshastighet är den linjära hastighet med vilken skärverktyget går in i arbetsstycket. Den mäts i tum per varv (IPR) eller millimeter per varv (mm/varv). För att optimera matningshastigheten, beakta faktorer som materialegenskaper, verktygsgeometri och önskad ytfinish. Högre matningshastigheter är i allmänhet mer produktiva men kan kräva kraftigare verktyg.
- c. Förhållande mellan skärhastighet och matningshastighet:Att balansera skärhastighet och matningshastighet är avgörande för effektiv materialborttagning. En ökning av skärhastigheten tillåter vanligtvis en högre matningshastighet, men de två måste justeras tillsammans för att förhindra verktygsslitage och överhettning.
2. Skärdjup:
- a. Skärdjup (DOC):Skärdjupet är det avstånd som skärverktyget tränger in i arbetsstycket. Det är viktigt att ta hänsyn till materialets och verktygets kapacitet. Optimera skärdjupet baserat på materialets hårdhet och verktygets styrka och styvhet. Grunda snitt kan vara nödvändiga för hårdare material, medan djupare snitt kan uppnås i mjukare material.
- b. Axialt och radiellt skärdjup:Vid CNC-svarvning, beakta både axiellt (längs arbetsstyckets längd) och radiellt (över arbetsstyckets diameter) skärdjup. Optimala djup för varje kommer att variera beroende på drift och material.
3. Skärvätskor och smörjmedel:
- a. Välja rätt skärvätska:Skärvätskor är viktiga för att avleda värme, minska friktionen och förbättra spånavgången. Välj lämplig skärvätska baserat på materialet och bearbetningsoperationen. Vattenlöslig kylvätska, mineraloljebaserad eller syntetisk kylvätska kan vara att föredra för olika material.
- b. Korrekt tillämpning:Applicera skärvätskor effektivt på skärområdet för att säkerställa tillräcklig smörjning och kylning. Detta kan göras genom översvämningskylning, dimsystem eller kylvätskeleverans genom verktyg, beroende på maskinens kapacitet.
- c. Övervakning och underhåll:Övervaka regelbundet skärvätskenivåer, tillstånd och kontaminering för att säkerställa att de förblir effektiva. Underhåll skärvätskesystem för att förhindra problem som bakterietillväxt och nedbrytning.
4. Verktygslivshantering:
- a. Verktygsinspektion och underhåll:Implementera ett rutinmässigt verktygsinspektions- och underhållsprogram för att säkerställa att verktygen är i gott skick. Slöa eller skadade verktyg kan resultera i dålig bearbetningskvalitet och minskad verktygslivslängd.
- b. Schema för verktygsbyte:Upprätta ett schema för verktygsbyte baserat på faktorer som verktygsslitage, maskindrifttid och produktionskrav. Detta hjälper till att förhindra oväntade verktygsfel och bibehåller konsekvent bearbetningskvalitet.
- c. Verktygslivsoptimering:Vissa verktygsmaterial och beläggningar ger längre verktygslivslängd. Överväg att använda högpresterande verktyg för att optimera verktygets livslängd och minska produktionsstopp.
- d. Verktygsspånkontroll:Effektiv spånkontroll, inklusive användning av spånbrytare och korrekt verktygsgeometri, kan förlänga verktygets livslängd genom att minska spåninducerat slitage.
Att optimera skärparametrar vid CNC-svarvning är en kontinuerlig process. Experiment och finjustering kan krävas för att hitta de bästa parametrarna för en specifik tillämpning. Övervaka och justera dessa parametrar regelbundet för att säkerställa optimal bearbetningsprestanda, verktygslivslängd och detaljkvalitet. Korrekt optimerade skärparametrar förbättrar inte bara bearbetningseffektiviteten utan minskar också verktygsslitage och, i slutändan, produktionskostnader.
Felsökning av vanliga problem i verktygsinställning
Felsökning av vanliga problem vid verktygsinställning är en viktig färdighet för maskinister och CNC-operatörer. Att förstå och ta itu med dessa problem kan hjälpa till att bibehålla precisionen och kvaliteten på bearbetningsoperationer. Här är några vanliga problem med verktygsinställning och deras lösningar:
1. Tool Chatter:
Problem: Verktygsflimmer uppstår när skärverktyget vibrerar under bearbetningsprocessen, vilket leder till dålig ytfinish, verktygsslitage och potentiell skada på arbetsstycket.
Lösning:
- Minska hastigheten eller öka matningen: Justera skärparametrarna genom att antingen minska skärhastigheten eller öka matningshastigheten. Denna förändring kan dämpa vibrationer och minska tjatter.
- Kontrollera verktygets styvhet: Se till att verktygshållaren och verktyget är korrekt säkrade och att verktyget inte sträcker sig för långt från hållaren.
- Kontrollera arbetsstyckets fastspänning: Se till att arbetsstycket är ordentligt fastklämt för att förhindra arbetsstyckesrelaterade vibrationer.
- Använd dämpningstekniker: Vissa maskiner kommer med funktioner för att dämpa vibrationer. Om det finns, överväg att använda dem.
- Välj ett styvare verktyg: Ett styvare verktyg, som ett med färre flöjter, kan hjälpa till att minska prat.
2. Dålig ytfinish:
Problem: En dålig ytfinish kan orsakas av problem med verktygsinställning eller skärparametrar, vilket leder till grova eller inkonsekventa ytor på arbetsstycket.
Lösning:
- Kontrollera verktygsgeometri: Se till att skärverktygets geometri är lämplig för operationen. Ett vasst verktyg med rätt geometri är avgörande för att få en bra ytfinish.
- Optimera skärparametrar: Justera skärhastighet, matningshastighet och skärdjup för att hitta den bästa kombinationen för det specifika materialet och operationen.
- Kontrollera verktygsslitage: Inspektera verktyget med avseende på tecken på slitage eller skador, såsom avhuggna kanter. Byt ut eller slipa om verktyget efter behov.
- Använd lämplig skärvätska: Korrekt smörjning och kylning kan avsevärt påverka ytfinishen. Använd rätt skärvätska för materialet och driften.
- Minimera vibrationer: Åtgärda vibrationsproblem för att undvika att skapa ojämnheter i ytan.
3. Dimensionella felaktigheter:
Problem: Delar kan ha felaktiga dimensioner på grund av felinriktade verktyg eller verktygsslitage.
Lösning:
- Kontrollera verktygsinställningar: Kontrollera att verktyget är korrekt inställt med rätt höjd och inriktning i förhållande till arbetsstycket.
- Kalibrera maskin: Se till att CNC-maskinen är korrekt kalibrerad och att den tolkar verktygsoffset och verktygsdata korrekt.
- Justera verktygsoffset: Korrigera eventuella fel i verktygsoffset genom att noggrant mäta verktyget och ange rätt offsetvärden i CNC-kontrollen.
- Inspektera verktygsslitage: Inspektera regelbundet skärverktyget för slitage och byt ut eller slipa om det vid behov.
4. Chipkontrollproblem:
Problem: Felaktig spånkontroll kan leda till problem som spåntilltäppning, dålig evakuering av spån och skador på arbetsstycket eller verktyget.
Lösning:
- Välj rätt verktygsgeometri: Välj ett skärverktyg med lämplig spånbrytare eller geometri för materialet och driften.
- Optimera skärparametrar: Justera matningshastigheter, skärhastigheter och skärdjup för att optimera spånbildning och evakuering.
- Använd adekvat smörjning: Korrekt användning av skärvätskor kan hjälpa till att smörja och underlätta evakueringen av spån.
- Kontrollera verktygets och arbetsstyckets inriktning: Se till att verktyget är korrekt inriktat med arbetsstycket för att förhindra spånrelaterade problem.
5. Verktygsbrott:
Problem: Verktygsbrott kan uppstå på grund av överdriven kraft, felaktig verktygsinställning eller materialrelaterade problem.
Lösning:
- Optimera skärparametrar: Minska skärkrafterna genom att justera parametrar som matningshastigheter, skärhastigheter och skärdjup.
- Kontrollera verktygsinställningar: Se till att verktyget är säkert monterat i verktygshållaren och att det är korrekt inriktat.
- Använd rätt verktygsmaterial: Välj rätt verktygsmaterial för det specifika material du bearbetar. Till exempel är hårdmetallverktyg bättre för hårda material.
- Inspektera för verktygsslitage: Kontrollera regelbundet verktyget för tecken på slitage och byt ut det innan det blir överdrivet slitet och benäget att gå sönder.
Att lösa dessa vanliga problem med verktygsinställning kräver en kombination av korrekt utbildning, regelbundet underhåll och ett systematiskt tillvägagångssätt för felsökning. Förmågan att diagnostisera och lösa verktygsrelaterade problem är avgörande för att uppnå högkvalitativa och effektiva bearbetningsresultat.
Slutsatser
Processen att ställa in och optimera svarvskärverktyg för CNC-svarvning är en avgörande aspekt av bearbetning som avsevärt påverkar kvaliteten, effektiviteten och precisionen i tillverkningsprocesser. En djup förståelse av komponenterna och funktionerna hos skärande verktyg, såväl som faktorerna som är involverade i verktygsval, är avgörande för maskinister och CNC-operatörer.
Att korrekt ställa in ett skärverktyg innebär ett systematiskt tillvägagångssätt, från att förbereda svarven och arbetsstycket till att välja rätt verktygshållare, montera verktyget, justera verktygshöjden och mittlinjeinriktningen och konfigurera verktygets nosradiekompensation och verktygsförskjutningar. Varje steg spelar en avgörande roll för att uppnå exakta och effektiva bearbetningsresultat.
Att optimera skärparametrar, inklusive hastigheter och matningar, skärdjup, skärvätskor och hantering av verktygets livslängd, är en annan kritisk aspekt av CNC-svarvning. Genom att noggrant välja rätt parametrar kan maskinister förbättra produktiviteten, behålla verktygets livslängd och förbättra ytkvaliteten.
Slutligen är det viktigt att kunna felsöka vanliga verktygsinställningsproblem, såsom verktygsklatter, dålig ytfinish, dimensionella felaktigheter, spånkontrollproblem och verktygsbrott för att bibehålla konsekventa och högkvalitativa bearbetningsresultat. Att identifiera dessa problem och implementera lämpliga lösningar säkerställer att bearbetningsprocessen förblir smidig och effektiv.
Sammantaget ger en omfattande förståelse för svarvskärverktyg och deras inställningar, i kombination med förmågan att optimera skärparametrar och felsöka problem, maskinister att uppnå de bästa resultaten i CNC-svarvningsoperationer. Kontinuerligt lärande, utbildning och erfarenhet är nyckeln till att förfina dessa färdigheter och säkerställa framgångsrika bearbetningsprocesser.
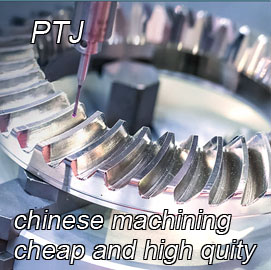
- 5 Axelbearbetning
- Cnc fräsning
- Cnc vändning
- Bearbetningsindustrin
- Bearbetningsprocess
- Ytbehandling
- Metallbearbetning
- Plastbearbetning
- Pulvermetallurgi mögel
- Matrisgjutning
- Reservdelsgalleri
- Auto metalldelar
- Maskindelar
- LED Kylfläns
- Byggnadsdelar
- Mobila delar
- Medicinska delar
- Elektroniska delar
- Skräddarsydd bearbetning
- cykeldelar
- Aluminiumbearbetning
- Titanbearbetning
- Bearbetning i rostfritt stål
- Kopparbearbetning
- Mässing
- Superlegering bearbetning
- Titta på bearbetning
- UHMW -bearbetning
- Unilate Bearbetning
- PA6 -bearbetning
- PPS -bearbetning
- Teflonbearbetning
- Inconel-bearbetning
- Verktygsstålbearbetning
- Mer material