Hur bearbetas högprecisionsdelar
2023-09-22
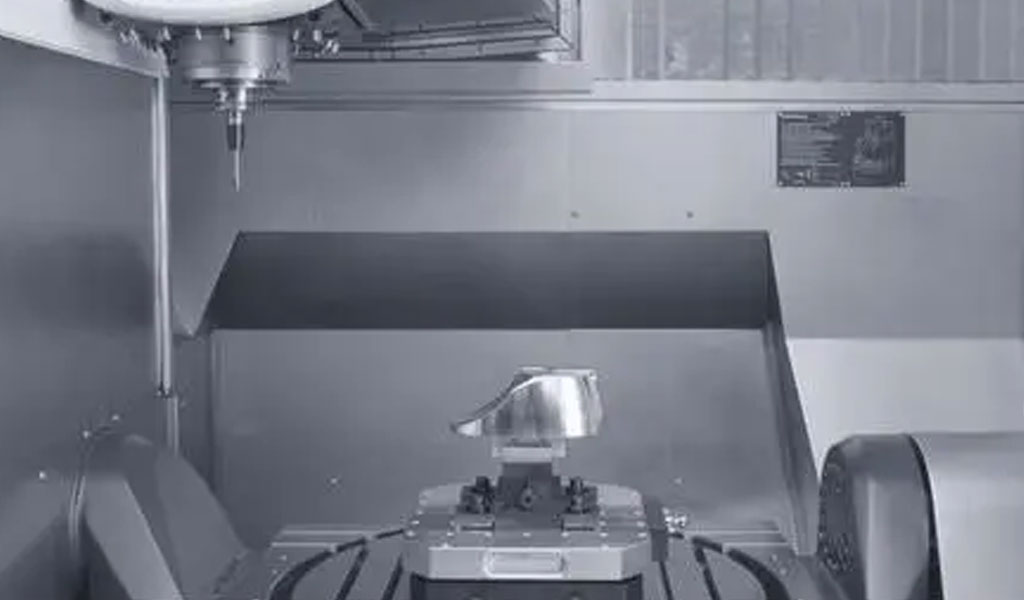
Förstå precisionsbearbetning
Precisionsbearbetning är en hörnsten i modern tillverkning, ansvarig för att producera intrikata och exakta komponenter som används i ett brett spektrum av industrier. För att förstå dess betydelse fullt ut, låt oss utforska kärnkoncepten för precisionsbearbetning, dess viktiga roll i olika sektorer och den historiska resan som har lett till dess nuvarande tillstånd av excellens.A. Vad är precisionsbearbetning?
Precisionsbearbetning hänvisar till en uppsättning tillverkningsprocesser som tar bort material från ett arbetsstycke med en hög grad av noggrannhet och kontroll, vilket resulterar i fint utformade komponenter med snäva toleranser. Denna process förvandlar råvaror, såsom metaller, plaster eller keramik, till exakta delar som uppfyller krävande specifikationer. De viktigaste egenskaperna hos precisionsbearbetning inkluderar:- Noggrannhet: Precisionsbearbetning säkerställer att slutprodukten överensstämmer exakt med den avsedda designen, med minimal avvikelse.
- Snäva toleranser: Det möjliggör tillverkning av delar med extremt snäva toleranser, vilket innebär att de färdiga komponenterna håller sig nära specificerade mått.
- Överlägsen ytfinish: Precisionsbearbetning ger exceptionell ytfinish, vilket ofta eliminerar behovet av ytterligare efterbehandlingsprocesser.
- Komplexa geometrier: Den kan skapa invecklade former, konturer och funktioner, vilket gör den oumbärlig vid tillverkning av komponenter med komplexa konstruktioner.
- Repeterbarhet: Precision bearbetningsprocesses är mycket repeterbara, vilket säkerställer konsekvent kvalitet över flera delar.
- Mångsidighet: Den kan appliceras på ett brett spektrum av material, vilket gör den lämplig för olika industrier.
B. Vikten av precisionsbearbetning
Precisionsbearbetning har en enorm betydelse i flera kritiska branscher, som påverkar olika aspekter av vårt dagliga liv. Här är några övertygande skäl till dess betydelse:- rymd~~POS=TRUNC: Inom flygsektorn är precisionsbearbetning oumbärlig för att tillverka komponenter som tål extrema förhållanden. Flygplansmotorer, landning kugghjulet, och strukturella element förlitar sig på precisionsbearbetade delar för säkerhet och prestanda.
- Medicintekniska produkter: Medicinsk utrustning som kirurgiska instrument, proteser och implanterbara enheter kräver precisionsbearbetning för biokompatibilitet, noggrannhet och patientsäkerhet.
- Fordonssektorn: Precisionsbearbetade delar är avgörande för bilindustrin för att säkerställa tillförlitlighet och effektivitet hos fordon. Komponenter som motordelar, transmissionssystem och bromsmekanismer är beroende av exakt bearbetning.
- Elektronik och halvledare: Precisionsbearbetning är avgörande vid produktion av mikroelektroniska komponenter och halvledarenheter, där små toleranser är absolut nödvändiga för funktionalitet.
- Energisektorn: Energiindustrin förlitar sig på precisionsbearbetning för produktion av kritiska delar som används vid kraftgenerering, inklusive turbiner, generatorer och transmissionskomponenter.
- Verktyg och formtillverkning: Precisionsbearbetning är avgörande vid tillverkning av verktyg och formar, som i sin tur används för att skapa otaliga andra produkter.
- Hemelektronik: Produktionen av smartphones, bärbara datorer och annan hemelektronik drar nytta av precisionsbearbetning för att säkerställa snygg design och optimal funktionalitet.
- Forskning och utveckling: Forskare och vetenskapsmän är beroende av precisionsbearbetade komponenter för experiment, prototyper och laboratorieutrustning.
C. Historiskt perspektiv
Resan med precisionsbearbetning går tillbaka till antika civilisationer, där skickliga hantverkare använde rudimentära verktyg för att forma material. Den precision som uppnåddes på den tiden var dock begränsad jämfört med samtida standarder.- Tidig precisionsbearbetning: Den industriella revolutionen på 18- och 19-talen markerade en avgörande period i utvecklingen av precisionsbearbetning. Uppfinningen av verktygsmaskiner, såsom svarvar och fräsmaskiner, revolutionerade tillverkningen genom att möjliggöra större noggrannhet och konsekvens.
- Andra världskriget: Precisionsbearbetning spelade en avgörande roll under andra världskriget, eftersom det var nödvändigt för att producera militär utrustning med den precision och enhetlighet som krävdes. Denna era bevittnade framsteg inom bearbetningstekniker och uppkomsten av nya material.
- Framsteg efter kriget: Efterkrigstiden såg en ökning av tekniska innovationer, inklusive användningen av datornumeriska styrmaskiner (CNC). CNC-bearbetning möjliggör automatiserade och mycket exakta operationer, vilket inleder en ny era av tillverkning.
- Den digitala tidsåldern: Integreringen av datorer och programvara i bearbetningsprocesser har ytterligare förhöjt precisionsbearbetningen. Moderna CNC-maskiner kan utföra komplexa operationer med oöverträffad noggrannhet, vilket gör dem oumbärliga i dagens tillverkningslandskap.
Material och deras betydelse
Material är grunden för precisionsbearbetning, och valet av rätt material spelar en avgörande roll i tillverkningen av högprecisionsdetaljer. I det här avsnittet kommer vi att fördjupa oss i vikten av att välja lämpliga material, förstå betydelsen av materialegenskaper och utforska de olika faktorerna som påverkar bearbetbarheten.A. Val av material
Valet av material vid precisionsbearbetning är ett avgörande beslut som direkt påverkar prestanda, hållbarhet och funktionalitet hos slutprodukten. Tillverkare måste överväga flera faktorer när de väljer material:- Material lämplighet: Materialet måste vara lämpligt för den avsedda användningen. Olika industrier och applikationer har olika krav, såsom temperaturbeständighet, korrosionsbeständighet och elektrisk ledningsförmåga.
- Mekaniska egenskaper: Mekaniska egenskaper som draghållfasthet, hårdhet och duktilitet är avgörande. Till exempel inom flyg- och rymdindustrin är material med hög draghållfasthet att föredra för strukturella komponenter.
- Termiska egenskaper: Vissa tillämpningar kräver material med utmärkt värmeledningsförmåga eller motstånd mot höga temperaturer. Detta är särskilt viktigt i industrier som kraftproduktion och elektronik.
- Korrosionsbeständighet: I miljöer där korrosion är ett problem är material med hög motståndskraft mot korrosion, såsom rostfritt stål eller titan, att föredra.
- Viktöverväganden: Branscher som bil- och flygindustrin prioriterar ofta lättviktsmaterial som aluminium- eller kolfiberkompositer för att minska bränsleförbrukningen och förbättra prestandan.
- Kostnadsbegränsningar: Kostnaden är en viktig faktor vid materialval. Högpresterande material kan vara dyra, så tillverkare måste hitta en balans mellan prestanda och kostnadseffektivitet.
- Regelefterlevnad: I branscher som sjukvård måste material uppfylla stränga regulatoriska standarder för biokompatibilitet och säkerhet.
- Tillgänglighet: Tillgången på material och deras källor påverkar också urvalet. Vissa specialiserade legeringar eller kompositer kan ha begränsad tillgänglighet.
B. Materialegenskaper
Att förstå materialens egenskaper är avgörande för precisionsbearbetning. Här är några viktiga materialegenskaper och deras betydelse:- DraghållfasthetDraghållfasthet mäter ett materials förmåga att motstå en dragkraft utan att gå sönder. Det är viktigt för strukturella komponenter och delar som utsätts för mekanisk belastning.
- Hårdhet: Hårdhet indikerar ett materials motståndskraft mot deformation och slitage. Hårda material är lämpliga för skärverktyg, medan mjukare material kan vara att föredra för vissa applikationer, som tätningar.
- formbarhet: Duktilitet hänvisar till ett materials förmåga att deformeras utan att gå sönder när det utsätts för dragpåkänning. Duktila material är lättare att forma men kanske inte lämpar sig för applikationer som kräver styvhet.
- Värmeledningsförmåga: Material med hög värmeledningsförmåga leder effektivt bort värme. Denna egenskap är avgörande i applikationer där temperaturkontroll är avgörande.
- Elektrisk konduktivitet: Elektrisk ledningsförmåga är väsentlig i elektronik och elektriska komponenter, där material måste underlätta flödet av elektricitet.
- Magnetiska egenskaper: Magnetiska egenskaper är betydande i industrier som elektromagnetik och elektronik, där material kan behöva vara ferromagnetiska eller icke-magnetiska.
- Kemisk resistans: Material måste motstå kemisk korrosion i miljöer där de utsätts för syror, baser eller andra frätande ämnen.
C. Bearbetningsfaktorer
Bearbetbarhet hänvisar till den lätthet med vilken ett material kan bearbetas, skäras eller formas. Det påverkas av olika faktorer, inklusive:- Materialhårdhet: Mjukare material är i allmänhet lättare att bearbeta, medan hårdare material kan kräva specialiserade verktyg och tekniker.
- Chipbildning: Bildandet och evakueringen av spån under bearbetning påverkar processens effektivitet och ytfinish.
- Verktygsslitage: Olika material kan orsaka varierande grad av verktygsslitage, vilket påverkar bearbetningshastigheten och kostnaden.
- Kylvätska och smörjning: Korrekt kylvätska och smörjning är avgörande för att minska friktion, värme och verktygsslitage under bearbetning.
- Skärhastighet: Hastigheten med vilken skärverktyget rör sig genom materialet påverkar både produktiviteten och kvaliteten på den bearbetade ytan.
- Verktygsmaterial: Valet av skärverktygsmaterial, såsom hårdmetall eller snabbstål, beror på materialet som bearbetas.
- Skärparametrar: Justering av skärparametrar som matningshastighet och skärdjup kan optimera bearbetningsprocessen för specifika material.
Verktygsmaskiner för precisionsbearbetning
Verktygsmaskiner är hjärtat av precisionsbearbetning, vilket möjliggör omvandling av råmaterial till högprecisionsdelar. I det här avsnittet kommer vi att utforska fyra nyckeltyper av verktygsmaskiner som används vid precisionsbearbetning: CNC-bearbetningscentra, svarvmaskiner, slipmaskiner och EDM (Electrical Discharge Machining). Var och en av dessa maskiner spelar en unik roll i tillverkningen av exakta komponenter.A. CNC-bearbetningscentra
CNC-bearbetningscenter (Computer Numerical Control) är mångsidiga och används i stor utsträckning vid precisionsbearbetning. De är automatiserade system som styr rörelsen av skärverktyg och arbetsstycken med exceptionell precision. Här är en översikt över CNC-bearbetningscentra och deras betydelse:- Mångsidighet: CNC-bearbetningscenter kan utföra olika bearbetningsoperationer, inklusive fräsning, borrning och gängning. Denna mångsidighet möjliggör tillverkning av komplexa delar med flera funktioner.
- Hög precision: Den datoriserade kontrollen av CNC-maskiner säkerställer exakt verktygspositionering och konsekventa resultat, vilket gör dem idealiska för delar med snäva toleranser.
- Automation: CNC-bearbetningscentra kan arbeta kontinuerligt, med minimal mänsklig inblandning. Denna automatisering ökar effektiviteten och minskar risken för fel.
- Komplexa geometrier: De utmärker sig i att bearbeta intrikata former och konturer, vilket gör dem lämpliga för industrier som flyg, där komplexa komponenter är vanliga.
- Upprepningsbara resultat: CNC-maskiner erbjuder utmärkt repeterbarhet, vilket säkerställer att varje tillverkad del matchar de exakta specifikationerna för designen.
- Reducerade installationstider: CNC-bearbetningscentra kan programmeras för att snabbt växla mellan olika uppgifter, vilket minimerar inställningstider och ökar produktionseffektiviteten.
B. Svarvmaskiner
Svarvmaskiner används för att skapa cylindriska delar genom att rotera ett arbetsstycke medan ett skärverktyg tar bort material från dess yttre yta. De är viktiga för att producera axels, stift och andra komponenter med rotationssymmetri. Viktiga punkter om svarvar inkluderar:- Cylindriska delar: Svarvmaskiner är specialiserade på att tillverka cylindriska eller rörformiga komponenter, inklusive de med gängor eller intrikata spår.
- Höga hastigheter: De arbetar i höga hastigheter, vilket gör dem lämpliga för delar som kräver en jämn och exakt finish.
- Enaxlig drift: De flesta svarvar är enaxliga och fokuserar på att forma arbetsstyckets yttre yta.
- Effektiv för massproduktion: Svarvning är mycket effektivt för masstillverkning av detaljer med minimalt materialspill.
- Svarvmaskiner: Manuella och CNC-styrda svarvar är vanliga svarvar som erbjuder en rad möjligheter.
C. Slipmaskiner
Slipmaskiner är konstruerade för precisionsbearbetning och formning av hårda eller abrasiva material. De är avgörande för att uppnå extremt snäva toleranser och överlägsen ytfinish. Här är varför slipmaskiner är viktiga:- Precision på mikronnivå: Slipmaskiner kan uppnå precision på mikronnivå, vilket gör dem viktiga för applikationer som kräver högsta noggrannhet.
- Materialborttagning: De tar bort material genom nötning, vilket möjliggör korrigering av ytfel och uppnår exceptionell jämnhet.
- Verktyg och fräs Slipning: Förutom ytslipning finns det specialiserade slipmaskiner för slipning av skärverktyg och framställning av exakta profiler.
- Olika slipmetoder: Olika typer av slipmaskiner, inklusive ytslipmaskiner, cylindriska slipmaskiner och centerless slipmaskiner, tillgodoser olika bearbetningsbehov.
- Härdade material: Slipning är särskilt lämplig för härdade material som verktygsstål och keramik, där traditionella bearbetningsmetoder kan vara ineffektiva.
D. EDM (Electrical Discharge Machining)
EDM, eller Electrical Discharge Machining, är en icke-traditionell bearbetningsprocess som använder elektriska urladdningar för att forma material. Den är idealisk för att skapa invecklade och ömtåliga delar där traditionella skärverktyg kan orsaka skada. Nyckelaspekter av EDM inkluderar:- Ingen fysisk kontakt: EDM involverar inte direkt fysisk kontakt mellan verktyget och arbetsstycket, vilket minimerar risken för verktygsslitage och skador på ömtåliga material.
- Hög precision: Den kan uppnå hög precision och ytfinishkvalitet, även med exceptionellt hårda material.
- Wire EDM och Sinker EDM: Det finns två primära typer av EDM-maskiner: trådskärning EDM, som använder en trådelektrod, och sinker EDM, som använder en formad elektrod.
- Komplexa former: EDM kan producera komplexa former, såsom stansar och formar, med intrikata detaljer och fina egenskaper.
- Värmepåverkad zon: Eftersom EDM inte genererar värme vid arbetsstycket, är det lämpligt för värmekänsliga material som flyglegeringar.
- Långsam process: EDM är relativt långsam jämfört med andra bearbetningsmetoder, vilket gör den bäst lämpad för jobb med låga kvantiteter och hög precision.
Skärverktyg och verktyg
Skärande verktyg ligger i framkant av precisionsbearbetning och fungerar som instrumenten som formar och omvandlar råmaterial till högprecisionsdelar. I det här avsnittet kommer vi att utforska de olika typerna av skärande verktyg, vikten av verktygsbeläggningar och de faktorer som påverkar verktygets livslängd och slitage.A. Typer av skärverktyg
Precisionsbearbetning förlitar sig på en mängd olika skärverktyg, var och en utformad för specifika uppgifter och material. Valet av skärverktyg påverkar i hög grad effektiviteten och noggrannheten i bearbetningsprocessen. Här är några vanliga typer av skärverktyg:- Slutverk: Pinnfräsar är mångsidiga verktyg som används för fräsoperationer. De har flera skäreggar och kan ta bort material från arbetsstycket på olika sätt, inklusive fasad, konturering och slitsning.
- borrar: Borrar är utformade för att skapa hål i arbetsstycken. De finns i olika former, inklusive spiralborrar, mittborrar och vändbara borrar.
- Vridande skär: Dessa används i svarvmaskiner för att forma cylindriska delar. Svarvskär finns i en mängd olika former och material för att passa olika applikationer.
- Frässkärare: Fräsar finns i olika former, såsom planfräsar, kulfräsar och spårfräsar, och används i fräsmaskiner för att skapa olika funktioner på arbetsstycket.
- brotschar: Bryttar används för att avsluta och dimensionera tidigare borrade hål till exakta mått. De säkerställer jämna och exakta hålytor.
- Tappar och dör: Dessa skärverktyg används för gängning. Kranar skapar inre gängor, medan stansar skapar yttre gängor.
- slip~~POS=TRUNC: Slipskivor är slipverktyg som används för precisionsslipning av ytor. De finns i olika slipmaterial och kornstorlekar.
- Broscher: Broscher är specialverktyg som används för att skära inre och yttre former och profiler, såsom kilspår och splines.
- Försänkningar och försänkningar: Dessa verktyg används för att skapa urtag eller avfasningar runt hål för fästanordnings.
- Tråkiga barer: Borrstänger används vid borrning för att förstora befintliga hål med precision.
B. Verktygsbeläggningar
Verktygsbeläggningar är tunna lager av material som appliceras på skärverktyg för att förbättra deras prestanda och hållbarhet. Dessa beläggningar erbjuder flera fördelar:- Minskad friktion: Beläggningar som titannitrid (TiN) och titankarbonitrid (TiCN) minskar friktionen mellan verktyget och arbetsstycket, vilket leder till mjukare skärning och längre livslängd.
- Förbättrad hårdhet: Beläggningar ökar hårdheten på verktygets yta, vilket gör det mer motståndskraftigt mot slitage och förlänger verktygets livslängd.
- Förbättrad värmebeständighet: Beläggningar tål höga temperaturer som genereras under bearbetning, vilket minskar värmerelaterat verktygsslitage och ökar skärhastigheterna.
- Anti-uppbyggnadsegenskaper: Vissa beläggningar har antividhäftningsegenskaper, vilket förhindrar ansamling av material på verktygets skäreggar.
- Ökad smörjförmåga: Belagda verktyg har förbättrad smörjförmåga, vilket minskar behovet av överdriven kylvätska och förbättrar spånavgången.
C. Verktygets livslängd och slitage
Att förstå verktygets livslängd och slitage är avgörande för att optimera bearbetningsprocesser och minimera produktionskostnaderna. Verktygets livslängd avser hur länge ett skärverktyg förblir effektivt innan det behöver bytas ut eller rekonditioneras. Flera faktorer påverkar verktygets livslängd och slitage:- Skärhastighet: Högre skärhastigheter kan leda till ökat verktygsslitage på grund av högre temperaturer som genereras under bearbetning. Rätt val av skärhastigheter är avgörande för att balansera verktygets livslängd och produktivitet.
- Flödeshastighet: Den hastighet med vilken skärverktyget förs in i arbetsstycket påverkar verktygsslitaget. Höga matningshastigheter kan påskynda slitaget, medan lägre matningshastigheter kan förlänga verktygets livslängd.
- Klippdjup: Skärdjupet påverkar mängden material som tas bort per passage. Djupare snitt kan öka verktygsslitaget, så att optimera djupet är avgörande.
- Materialhårdhet: Kapning av hårda material kan påskynda slitaget på verktyg. Specialverktyg och beläggningar används för effektiv bearbetning av hårda material.
- Kylvätska och smörjning: Korrekt kylvätska och smörjning hjälper till att avleda värme och minska friktionen, vilket förlänger verktygets livslängd.
- Verktygsmaterial: Materialet som skärverktyget är tillverkat av påverkar dess slitstyrka. Material som hårdmetall och keramik ger utmärkt slitstyrka.
- Verktygsgeometri: Skärverktygets geometri, inklusive spånvinkel, avlastningsvinkel och spånbrytardesign, spelar en betydande roll för slitagemönster.
- Arbetsstyckets material: Den typ av material som bearbetas påverkar verktygsslitaget. Slipande material kan leda till snabbare verktygsslitage.
Precisionsbearbetningsprocesser
Precisionsbearbetningsprocesser är metoderna genom vilka råmaterial omvandlas till högprecisionsdetaljer med snäva toleranser och exceptionell ytfinish. I det här avsnittet kommer vi att utforska fem viktiga precisionsbearbetningsprocesser: svarvning, fräsning, borrning, slipning och elektrisk urladdningsbearbetning (EDM). Var och en av dessa processer tjänar ett unikt syfte och används baserat på arbetsstyckets specifika krav.A. Vändning
Svarvning är en bearbetningsprocess som främst används för att forma cylindriska delar. Det innebär att ett arbetsstycke roteras medan ett enpunkts skärverktyg tar bort material från den yttre ytan. Här är de viktigaste aspekterna av svarvning:- Cylindriska delar: Svarvning är idealisk för tillverkning av cylindriska komponenter som axlar, stift och hylsor.
- Rotationssymmetri: Den är väl lämpad för delar som kräver rotationssymmetri, eftersom arbetsstycket roterar på en svarv medan skärverktyget formar det.
- Olika operationer: Svarvning kan utföra olika operationer, inklusive vändning, svarvning (minska diametern), konisk svarvning och gängning.
- Enpunktsskärning: Ett enda skärverktyg tar bort material i en kontinuerlig rörelse, vilket resulterar i effektiv materialborttagning.
- Svarvmaskiner: Både manuella och CNC-styrda svarvar används vanligtvis för svarvningsoperationer.
B. Fräsning
Fräsning är en mångsidig precisionsbearbetningsprocess som använder flerpunktsskärverktyg för att ta bort material från ett arbetsstycke. Den är väl lämpad för att skapa ett brett utbud av former och funktioner. Nyckelaspekter av fräsning inkluderar:- Mångsidighet: Fräsning kan ge plana ytor, slitsar, fickor och komplexa konturer. Den används för både 2D- och 3D-bearbetning.
- Flerpunktsskärning: Flera skäreggar på verktyget samverkar med arbetsstycket samtidigt, vilket möjliggör effektiv materialborttagning.
- Typer av fräsning: Fräsning kan utföras med olika typer av fräsar, inklusive pinnfräsar, planfräsar och kulfräsar.
- CNC-bearbetningscenter: CNC-styrda fräsmaskiner erbjuder exakt kontroll över verktygsrörelser och används ofta i modern bearbetning.
- Höga hastigheter: Fräsning kan utföras med höga hastigheter, vilket möjliggör effektiv produktion.
C. Borrning
Borrning är en precisionsbearbetningsprocess som används för att skapa hål i arbetsstycken. Det är en grundläggande verksamhet inom olika branscher. Viktiga aspekter av borrning inkluderar:- Skapande av hål: Borrmaskiner använder specialverktyg som kallas borrar för att ta bort material och skapa hål med specifika diametrar.
- Typer av borrar: Olika typer av borrmaskiner finns tillgängliga, inklusive spiralborrar, centrumborrar och vändbara borrar, var och en designad för specifika applikationer.
- Noggrannhet: Exakt positionering och inriktning är avgörande vid borrning för att säkerställa att hål skapas med noggrannhet.
- Hastighet och matningshastighet: Borrparametrar som rotationshastighet och matningshastighet är kritiska för att uppnå önskade håldimensioner.
- Kylvätska och smörjning: Korrekt kylvätska och smörjning används för att avleda värme och minska friktionen under borrning.
D. Slipning
Slipning är en precisionsbearbetningsprocess som använder slipskivor för att ta bort material och uppnå extremt snäva toleranser och ytfinish. Nyckelaspekter av slipning inkluderar:- Exceptionell precision: Slipning kan uppnå precision på mikronnivå, vilket gör den idealisk för applikationer som kräver högsta noggrannhet.
- Ytfinish: Den ger överlägsen ytfinish, vilket ofta eliminerar behovet av ytterligare efterbehandlingsprocesser.
- material: Slipning är lämplig för hårda och abrasiva material, inklusive härdat stål, keramik och karbider.
- Olika slipmetoder: Olika typer av slipmaskiner, såsom ytslipmaskiner, cylindriska slipmaskiner och centerless slipmaskiner, tillgodoser olika bearbetningsbehov.
- Kylvätska: Rätt kylvätska är avgörande vid slipning för att förhindra överhettning och bibehålla hjulets integritet.
E. Elektrisk urladdningsbearbetning (EDM)
EDM, eller Electrical Discharge Machining, är en icke-traditionell precisionsbearbetningsprocess som använder elektriska urladdningar för att avlägsna material. Den är särskilt lämpad för bearbetning av komplexa och intrikata former, såväl som hårda och värmebeständiga material. Nyckelaspekter av EDM inkluderar:- Bearbetning utan kontakt: EDM innebär inte direkt kontakt mellan verktyget och arbetsstycket, vilket minskar risken för verktygsslitage och skador.
- Hög precision: EDM kan uppnå hög precision, vilket gör den lämplig för applikationer där snäva toleranser är väsentliga.
- Komplexa former: Den utmärker sig vid bearbetning av komplexa former, formar, formar och komponenter med fina detaljer.
- Wire EDM och Sinker EDM: Det finns två primära typer av EDM-maskiner: tråd-EDM, som använder en trådelektrod, och sinker-EDM, som använder en formad elektrod.
- Långsam process: EDM är relativt långsam jämfört med andra bearbetningsmetoder, vilket gör den bäst lämpad för jobb med låga kvantiteter och hög precision.
Toleranser och kvalitetskontroll
Precisionsbearbetning kräver noggrann uppmärksamhet på detaljer och ett rigoröst engagemang för kvalitetskontroll för att säkerställa att delar uppfyller de specificerade standarderna. I det här avsnittet kommer vi att utforska tre kritiska aspekter av kvalitetskontroll inom precisionsbearbetning: Geometrisk dimensionering och tolerans (GD&T), Statistisk processkontroll (SPC) och kvalitetssäkring.A. Geometrisk dimensionering och tolerans (GD&T)
Geometrisk dimensionering och tolerans, ofta förkortat GD&T, är ett system som används för att definiera och kommunicera de tillåtna variationerna i storlek, form, orientering och placering av detaljer på en del. GD&T är avgörande för precisionsbearbetning av följande skäl:- Exakt kommunikation: GD&T tillhandahåller ett standardiserat språk för ingenjörer, designers och maskinister för att kommunicera designavsikter och dimensionskrav exakt.
- Toleransförtydligande: Det hjälper till att definiera den acceptabla variationen i kritiska dimensioner, vilket säkerställer att alla intressenter förstår de tillåtna avvikelserna.
- Förbättrad kvalitet: GD&T främjar förbättrad kvalitet genom att minska otydligheten i designspecifikationerna, vilket minimerar risken för fel under bearbetningen.
- Kostnadseffektivitet: Tydliga GD&T-specifikationer kan leda till minskade tillverkningskostnader, eftersom det är mindre sannolikt att delar skrotas eller kräver omarbetning på grund av missförstånd eller feltolkningar.
- Komplex geometri: Det är särskilt användbart för detaljer med komplexa geometrier, vilket säkerställer att alla funktioner tillverkas enligt önskade specifikationer.
B. Statistisk processkontroll (SPC)
Statistisk processkontroll (SPC) är en kvalitetskontrollmetod som använder statistiska tekniker för att övervaka och kontrollera bearbetningsprocessen. SPC är viktigt vid precisionsbearbetning av följande skäl:- Processövervakning: SPC hjälper till att övervaka bearbetningsprocesser i realtid, identifiera variationer eller avvikelser från de önskade parametrarna.
- Tidig upptäckt av problem: Genom att kontinuerligt övervaka processen möjliggör SPC tidig upptäckt av problem som kan leda till delar som inte är specifika för specifikationerna, vilket minskar avfall och omarbetning.
- Datadrivet beslutsfattande: SPC förlitar sig på data och statistisk analys för att fatta välgrundade beslut om processjusteringar, vilket säkerställer att bearbetningsprocessen förblir inom acceptabla gränser.
- Förbättrad konsistens: SPC främjar processkonsistens och minskar sannolikheten för tillverkning av delar som inte överensstämmer.
- Minskad skrot och omarbetning: Genom att snabbt identifiera och åtgärda processvariationer minimerar SPC produktionen av defekta delar, vilket minskar skrot- och omarbetningskostnader.
C. Kvalitetssäkring inom precisionsbearbetning
Kvalitetssäkring inom precisionsbearbetning omfattar ett heltäckande tillvägagångssätt för att säkerställa att tillverkade delar uppfyller eller överträffar specificerade kvalitetsstandarder. Det involverar olika element, inklusive:- Processdokumentation: Detaljerad dokumentation av bearbetningsprocesser, inklusive standarddriftsprocedurer (SOP) och arbetsinstruktioner, säkerställer att varje steg utförs konsekvent.
- Besiktning och mätning: Noggrann inspektion och mätning med hjälp av precisionsinstrument och mättekniker verifierar att delar överensstämmer med specificerade toleranser och kvalitetsstandarder.
- Kalibrering: Regelbunden kalibrering av bearbetningsutrustning och mätinstrument är avgörande för att upprätthålla noggrannhet och spårbarhet.
- Materialverifiering: Verifiering av materialegenskaper, sammansättning och kvalitet är avgörande för att säkerställa att materialet som används uppfyller designkraven.
- Utbildning för anställda: Utbildnings- och kompetensutvecklingsprogram för maskinister och kvalitetskontrollpersonal säkerställer att de är skickliga i sina roller och ansvarsområden.
- Grundorsaksanalys: När delar som inte överensstämmer identifieras, utförs rotorsaksanalys för att fastställa källan till problemet och implementera korrigerande åtgärder.
- Kontinuerlig förbättring: En kultur av ständiga förbättringar främjar innovation och driver pågående förbättringar av bearbetningsprocesser och kvalitetskontrollprocedurer.
- Kundrespons: Att samla in och analysera kundfeedback hjälper till att identifiera förbättringsområden och anpassar bearbetningsprocesser med kundernas förväntningar.
Slutsats
A. Konsten och vetenskapen om precisionsbearbetning
Precisionsbearbetning står i skärningspunkten mellan konst och vetenskap, där kreativitet, skicklighet och innovation möts för att producera högprecisionsdelar som driver industrier och formar den moderna världen. Det är både en konstform som kräver hantverk och expertis från maskinister som omvandlar råmaterial till verk av ingenjörsexpertis, och en vetenskap som förlitar sig på banbrytande teknik, materialvetenskap och avancerade processer för att uppnå oöverträffad precision. Resan med precisionsbearbetning tar oss genom förståelsen av material och deras egenskaper, behärskning av skärande verktyg och maskiner, och noggrann kontroll av processer och toleranser. Det omfattar språket för geometrisk dimensionering och tolerans, vaksamheten för statistisk processkontroll och engagemanget för kvalitetssäkring. Precisionsbearbetning spelar en avgörande roll i olika industrier, från flyg- och bilindustrin till medicinsk utrustning och elektronik, och formar allt från flygplansmotorer till konstgjorda leder och mikrochips. Det möjliggör skapandet av komponenter som fungerar med oöverträffad noggrannhet och tillförlitlighet, som ofta tänjer på gränserna för vad som är möjligt.B. Slutliga tankar
När vi avslutar denna utforskning av precisionsbearbetning är det tydligt att detta område inte bara handlar om att skapa delar; det handlar om att skapa möjligheter. Strävan efter precision driver innovation och tänjer på gränserna för vad som kan uppnås. Oavsett om det är det känsliga hantverket som krävs för att skapa en klockas intrikata växlar eller den avancerade tekniken som behövs för att tillverka komplexa flyg- och rymdkomponenter, är precisionsbearbetning kärnan i alltihop. Framtiden för precisionsbearbetning är fylld med löften. Framsteg inom materialvetenskap, automation och digital teknik fortsätter att omforma landskapet. Miniatyrisering, 3D-utskrift och hållbara tillverkningsmetoder blir allt mer framträdande, vilket inleder nya horisonter för branschen. I en värld där precision är viktigare än någonsin, förblir precisionsbearbetning en oumbärlig pelare i modern teknik. Det är ett bevis på mänsklig uppfinningsrikedom och vår orubbliga strävan efter excellens inom alla aspekter av tillverkningen. När efterfrågan på högre precision och mer invecklade komponenter växer, kommer precisionsbearbetning att fortsätta att utvecklas och möta morgondagens utmaningar med samma hängivenhet och precision som har definierat den i århundraden.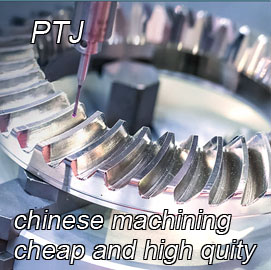
Våra tjänster
- 5 Axelbearbetning
- Cnc fräsning
- Cnc vändning
- Bearbetningsindustrin
- Bearbetningsprocess
- Ytbehandling
- Metallbearbetning
- Plastbearbetning
- Pulvermetallurgi mögel
- Matrisgjutning
- Reservdelsgalleri
Fallstudier
- Auto metalldelar
- Maskindelar
- LED Kylfläns
- Byggnadsdelar
- Mobila delar
- Medicinska delar
- Elektroniska delar
- Skräddarsydd bearbetning
- cykeldelar
Materiallista
- Aluminiumbearbetning
- Titanbearbetning
- Bearbetning i rostfritt stål
- Kopparbearbetning
- Mässing
- Superlegering bearbetning
- Titta på bearbetning
- UHMW -bearbetning
- Unilate Bearbetning
- PA6 -bearbetning
- PPS -bearbetning
- Teflonbearbetning
- Inconel-bearbetning
- Verktygsstålbearbetning
- Mer material
Reservdelsgalleri